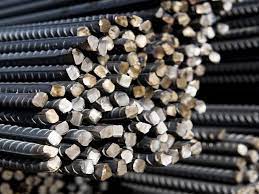
With long steel prices in Europe reaching historically high levels, construction activity is slowing in some regions due to reduced supplies and delays, with some market sources fearing a decline in industrial activity long term.
Surging prices
Long steel prices in the European Union started increasing in the third quarter of 2020 on a pick-up in consumption and a recovery from the impact of the Covid-19 pandemic.
Since Covid-related restrictions in Europe were eased, demand for construction steel such as beams, sections and rebar has remained solid, with reports of filled order books at mills pushing prices to historical peaks.
Since Covid-related restrictions in Europe were eased, demand for construction steel such as beams, sections and rebar has remained solid, with reports of filled order books at mills pushing prices to historical peaks.
In May this year, Fastmarkets’ price assessment for steel reinforcing bar (rebar), domestic, delivered Northern Europe averaged €730 ($892.94) per tonne, up sharply from the monthly average of €471.25 per tonne in May 2020, and its highest since August 2008.
The uptrend in prices has continued into June, with the most recent assessment of domestic rebar, delivered Northern Europe hitting €800-820 per tonne on June 9.
Meanwhile, the monthly average price of steel beams domestic, delivered Northern Europe has also risen to €850-872.50 per tonne in May, from €522-550 per tonne in July 2020. Prices recently touched €1,000 per tonne on June 9.
The short-term prospects for the sector are positive, with prices expected to continue rising amid short supply and strong demand. But sources are worried about the long-term effects of the price surge.
“Old projects currently under way must be completed, so construction is moving on. But we see a potential slowdown in new projects because costs are double what [construction] firms budgeted at the beginning of the year,” a German trader said.
Sources noted that some construction sites, especially in the private sub-sector, have started to slow activity and delay project end dates because they are unable to digest the surging prices for building materials, including steel.
“Demand is still good. But there are some voices from construction companies saying that at current prices, they will not start new projects and will put them on hold till September,” a trader in Poland told Fastmarkets.
“Construction activities are slowing down a bit. Some sites are delaying the date of [completion], expecting building materials’ prices will decline. But I do not think this is going to happen any time soon,” a trader in Italy said.
Most sources agreed that prices are yet to touch a ceiling.
“[EU] mills are very well booked; they have practically no stocks and neither do buyers. So buyers have to swallow the prices European mills are giving because there is no alternative,” one trader in the Netherlands said.
“Mills are rolling at full capacity to fulfill orders and lead times are a little bit longer than usual,” a second trader in the Netherlands said.
Feedstock costs
In the international market, prices for the feedstock material of beams and rebar – ferrous scrap – have also jumped over the past year.
Fastmarkets’ steel scrap HMS 1&2 (80:20 mix) North Europe origin, cfr Turkey averaged $496.52 per tonne last month, almost double June 2020’s average of $254.36 per tonne. The price has risen above $500 per tonne several times – a 10-year high.
This trend has also been reflected in Europe, where scrap prices increased across various grades driven by material shortages.
Fastmarkets’ monthly price assessment for steel scrap, E8 thin new production steel, domestic, delivered consumer, Germany was €460-500 per tonne on June 11, up by €50-80 per tonne from €410-420 per tonne in mid-May. The assessment has nearly doubled from €245-250 per tonne in June last year.
The impact of rising feedstock costs has been apparent in industry purchase managers’ index (PMI) surveys, with the IHS Markit construction PMI rating for the eurozone reporting growth for Italy and France for May, but not Germany.
The surveyed countries all cited higher raw material prices due to shortages among suppliers, and supply disruptions linked to delays caused by raw material shortages, including metals.
Germany’s PMI survey reported decreases in May and April due to supply bottlenecks, unprecedented delays in material delivery and sharp cost increases, with a continued reduction in new work being reported.
Germany’s PMI survey reported decreases in May and April due to supply bottlenecks, unprecedented delays in material delivery and sharp cost increases, with a continued reduction in new work being reported.
Construction industry response
Last month, the president of the European Construction Industry Federation (FIEC) wrote to the European Commission (EC) to express “alarm about the significant price increases in construction-related raw materials and products that are currently adversely affecting construction companies throughout the European Union.”
The letter said the situation was jeopardizing the construction sector’s contribution to economic recovery and the potential impact of European recovery programmes.
As well as the price increases, companies are experiencing delivery delays, with suppliers reluctant to agree a specific delivery deadline, and as a result construction companies cannot confirm the final price for their completed works and services.
The letter cited the pandemic as one issue, in addition to the delayed redistribution of unused steel, a malfunctioning international supply chain and trade policy as other factors.
Construction companies’ involvement in public contracts is also being severely hampered, with contractors bearing the burden of the price increases.
The resulting impact of inflation is also a risk that it could hinder projects in the national recovery plans, it said.
Projects funded by the EU, and those financed by the Next Generation EU Recovery Plan, mean the EC has a role to play, the letter said, while calling on member states to implement sensible price revision mechanisms for ongoing contracts and to be alert to opportunistic behavior.
As part of the recovery from the pandemic, the EU announced funding of €750 billion ($908 billion) for its Next Generation EU Recovery Plan to support member states. But one long steel producer source said that money has not yet been invested.
“This is something that is a risk – it’s not happening today. All the buyers say at this level the supply chain will stop and the end consumer will postpone investments,” the producer source said. “There is a recovery plan that has billions of euros not invested yet. The market will find its balance as demand-offer is unbalanced. It’s hard to think in a few months things will change dramatically.”
“Unprecedented surges in all building material costs pose a long-term threat for the [construction] industry. The costs of construction projects has nearly doubled from what was planned at the end of 2020,” a source in the construction industry said.
Strabag International, one of Europe’s largest construction companies, is experiencing delays at its sites due to poor material availability, according to chief executive officer Thomas Birtel.
“Prices have been rising sharply since the beginning of the year, especially for wood, copper, steel and polymers used for insulation and in sewer pipes, for example. In the past two weeks, the price dynamics have increased immensely. Strabag must now also report delays at individual construction sites because the materials are simply no longer available,” Birtel told Fastmarkets.
“Prices have been rising sharply since the beginning of the year, especially for wood, copper, steel and polymers used for insulation and in sewer pipes, for example. In the past two weeks, the price dynamics have increased immensely. Strabag must now also report delays at individual construction sites because the materials are simply no longer available,” Birtel told Fastmarkets.
“Looking to the long term, we see this as confirmation of our strategy of having our own dense network of raw materials, with concrete plants, quarries and asphalt plants. But construction is a compartmentalized business and it is not possible to control the supply chains for all construction materials,” he said.
“In view of the price developments, we have already indicated in our outlook for 2021 that it will not be possible to repeat the record margin of [earnings before interest and tax] of 4.3% on revenue that had been achieved in the previous year,” he added.
Delays are a possibility prices change sharply, a mill source told Fastmarkets, adding that it also depends on what percentage of the project costs comes from steel.
“A shortage is a good thing for producers – it’s only going to keep prices moving up. Buyers are worried about being able to get the steel, and with a project at 95% completion, if you need 2,000 tonnes to finish, you will be ready to pay anything to get hold of the material and it adds to customers’ worry,” the mill source said.
Lack of imports alternative
The lack of imports due to safeguarding measures in place has also supported long-steel price rises, sources said.
Before the introduction of the safeguard measures on 26 steel products imported into the European Union in 2019, imports accounted for a 30% share of rebar consumption in Germany and the Benelux area. After the restrictions were imposed, this figure fell to 5%, International Rebar Producers & Exporters Association (Irepas) said on June 4.
On Friday June 11, the EC presented a draft document of the adjusted measures to member states suggesting a three-year extension to the existing safeguard measures, and an increase to quota volumes of 3% year on year – lower than the 5% rise expected by market participants.
The 3% quota liberation was not well received by European buyers.
The 3% quota liberation was not well received by European buyers.
“In a market where consumption is booming, a 3% increase is not a liberalization, but rather a deterioration of the situation,” a source in Benelux area said.
“This is a disaster. EU steel imports have already declined substantially over the past three years because of safeguards. Importing is already a nightmare and the nightmare is here to stay,” a trading source in the EU said.
Total volumes of steel rebar imports into the EU declined to about 989,339 million tonnes in 2020, down by 36% from 1.55 million tonnes in 2019, according to data released by the European steel association, Eurofer.
Read full article at Metal Bulletin